Ever wonder how the latest Kinze innovations become reality, from idea to final product? Our proto, tool and die department is responsible for bringing new product designs to life. They are a team of fabricators, welders, tooling designers, machinists and assemblers that produce the first test units, and work hand-in-hand with test and design engineers to refine products before the latest technologies like Blue Drive are delivered to you. Not only that, but they also support existing product production by designing and building solutions that improve efficiency, quality and safety.
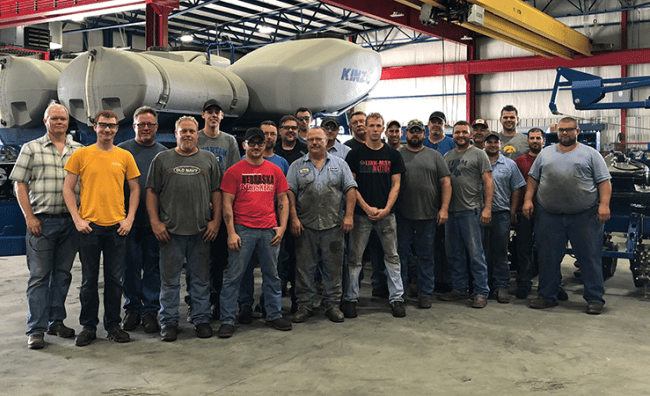
New Product Development
A new product idea is approved and the design is ready to go. What’s next? That is where the proto, tool and die team comes in. They create the first concept unit working hand-in-hand with the design engineer(s). The concept unit is reviewed then handed to the test department for rigorous testing, and improved as needed. This cycle could take up to several years before it’s approved for full production.
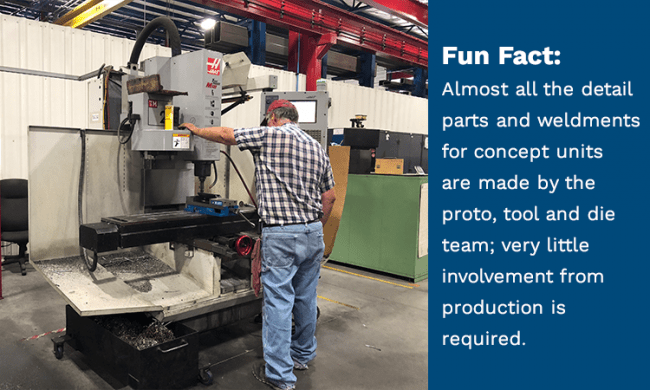
Once the concept product has been tested and approved for production, manufacturing prototype runs begin. Manufacturing engineers determine best manufacturing processes for that unit. Multiple units covering many configurations are built. At this point, necessary tooling for full production is established.

From there, pre-production begins, testing all the new tooling fixtures and ensuring tooling works for all configurations. If pre-production is successful, full production begins.
Exisiting Production Tool Support
After a new product is in full production, the proto, tool and die team’s job is done, right? Not so fast. Proto, tool and die also support ongoing production needs. Has manufacturing discovered a better way to manufacture a part that requires a new machine or press? Does a die (a cookie cutter for metal) need to be re-worked or adjusted? Manufacturing engineers and production staff work with proto, tool and die to create the machines or tooling necessary to fulfill any such manufacturing need. Below are a few examples.
Gauge Wheel Arm Press
A press designed by the Kinze proto, tool and die team to press bushings and seals in gauge wheel arms. “I like how efficient it is. You can do multiple arms at a time,” commented Levi H., small assembly supervisor.
Hitch Anchor for Mach Till Assembly
The Mach Till has a negative hitch weight and requires a tractor to anchor it to prevent tipping. This anchor was designed by Dan G., a proto technician. “This anchor eliminates the need for tractor and allows room for one more station for greater production efficiency,” explained Billy S., group lead for Mach Till assembly.

Individual Row Unit and Multi Unit Transport Carts
These carts transport row units from small assembly to where they are needed in assembly. “I like the readiness to assemble the row unit on the toolbar,” said Tyler D., large assembly.
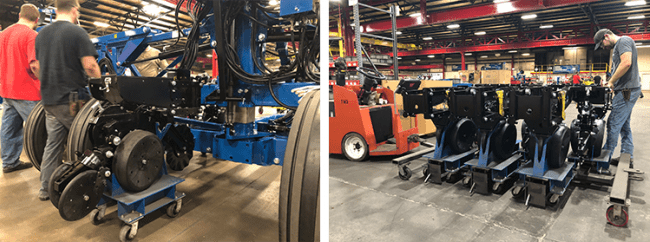
You can see many of the improvements our proto, tool and die department has made throughout production on a factory tour. And when you see a Kinze product operating in the field, know that this team is part of bringing it to the field from nearly the beginning stages.