It can be argued that the single biggest factor in determining whether a farmer is successful is the weather. A wet, muddy fall in 1970 led one corn farmer to ask Jon Kinzenbaw to come up with a new way of getting grain from the combine to the truck. So, in Jon’s own words, here is the story of the first grain cart built 50 years ago in 1971.
Our first grain wagon, the forerunner of the grain cart, was a four-wheeled version that I built in 1967 for the late Wayne Butler of Ladora, Iowa. It was originally intended to hold 400 bushels but was later extended to 600-bushel capacity. A PTO-driven transmission and rear axle assisted the heavily-loaded wagon in soft fields; an auger unloaded it at the rear. With the transmission in fifth gear, this wagon would “push” the tractor down the road at 30 mph with the tractor transmission in neutral. The “Kinze” brand was hand-painted with a four-inch brush.
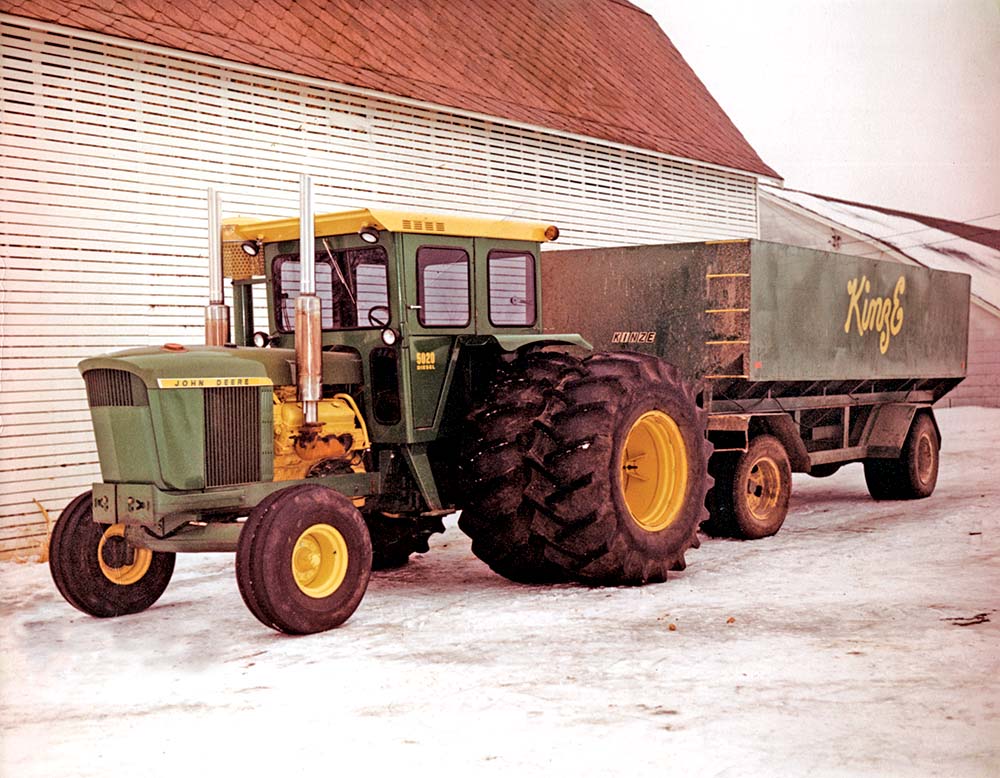
In the next few years, as we were custom applying anhydrous with the new applicator and re-powers, Bob Walker was one of our biggest customers. He came into the shop in early 1971 and talked about how wet the previous fall had been and how the fields were too muddy for trucks to get to where the combines were and unload them. It was very time consuming to drive a combine back and forth to where a truck was parked at the edge of the field or on the road. Bob said, “I’d like to have you make a conveyor or an auger on a John Deere tractor that has a receiving hopper on the back end. The auger has to run up over the front end, so make it long enough that we can park the tractor at the edge of the field and elevate corn across the road ditch and into the truck sitting on the road. You think you could build something like that?” And I said, “Well, yeah, I’m sure we could.” So we discussed that a few times, but at some point he said, “I’ve got a different idea. I think we need a big wagon.” He went on to tell me about some big diamond-tread tires he bought off a hillside combine. He said, “I thought they looked like they might be interesting to build something out of, so I’ll bring them in.”
Bob said he’d heard of a company in Milton, Iowa, that was building a big auger wagon, so we drove there to take a look. It was a small welding shop, and they had three prototypes, but they were a hodgepodge. It looked like they cut steel into as many pieces as they could and then turned around and welded them all back together. They offered to sell Bob a prototype so that we could take it back to my shop and finish it. But after looking at it, I said, “Bob, I think we can build one ourselves from scratch easier than we can mess with something like that.” On the drive back, Bob said he wanted me to build a two-wheeled cart that would hold at least 400 bushels. “I want it to unload fast, and I want you to use those diamond-tread tires.”
Unloading fast meant a large auger. I had studied augers and had been repairing them for farmers. Most of them were four or six inches in diameter. Occasionally, we’d run across what we would call a “monster,” an eight-inch auger. But based on the speed at which they unloaded, I calculated in my mind that a 12-inch auger would be about right for a 400-bushel grain cart.
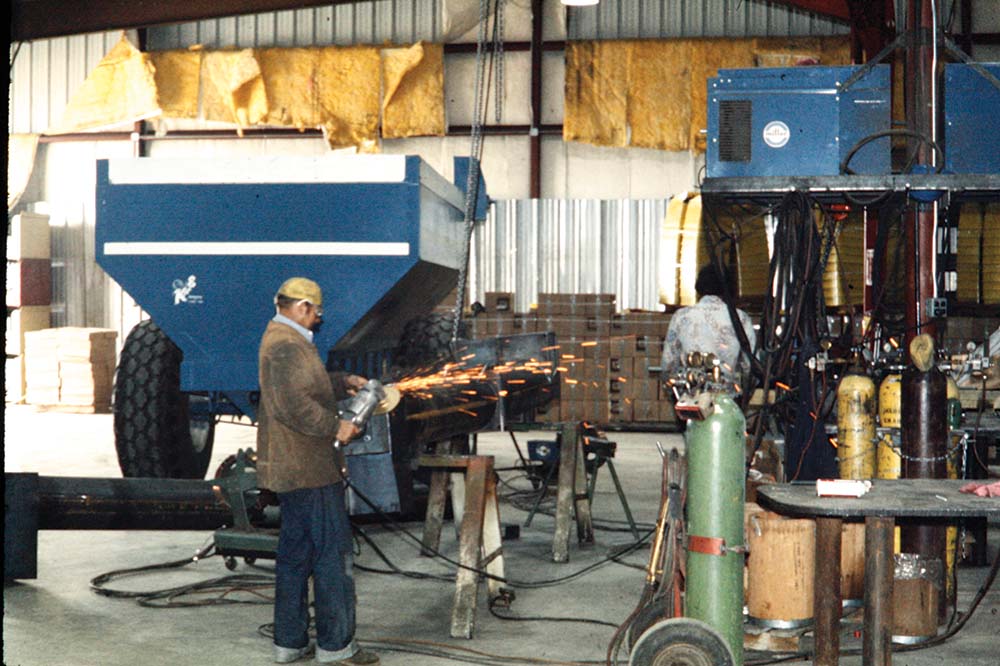
Working on the 400-bushel grain cart
I also knew that a horizontal auger would carry a lot more corn than a vertical auger, so the auger in the floor of the cart had to be smaller than the one that went up in the air. When I talked to the people at Newell Machinery in Cedar Rapids, they said a nine-inch auger feeding a 12-inch would be about right, and I could run them both at the same speed. But when I said, “I want to run it at power take-off speed (540 rpm),” they said that was too fast. I asked why. They said they didn’t know, but 140 rpm was the recommended maximum speed. Well, we had a Heider auger wagon with a six-inch auger that ran at 540 rpm all the time, so I bought the augers and went away thinking I was going to prove a point. We built the entire cart with a nine-inch floor auger and a 12-inch vertical auger on the assumption it was going to work at PTO speed.
We started on the cart in the late spring of 1971 to have it ready for fall harvest. The frame was made out of eight-inch and 10-inch channel iron, and we boxed it together. I got Henderson Metal to cut some basic pieces of sheet metal to form the “V” part of the tub, the body. And it looked a lot like the carts we still build today in terms of shape and configuration. The nine-inch auger in the floor came forward and fed into the 12-inch auger. As I recall, we used a gear box off an old International No. 2-MH corn picker. It had a 1:1 ratio gear box at the back end, and that’s how I accomplished the right-angle box to drive the vertical auger. At first, I thought it needed a clutch in order to release the horizontal auger, but we quickly found it wasn’t important because you could start and stop the auger with the 540 rpm power take-off just fine. That cart unloaded itself in something like three minutes, unheard of at that time.
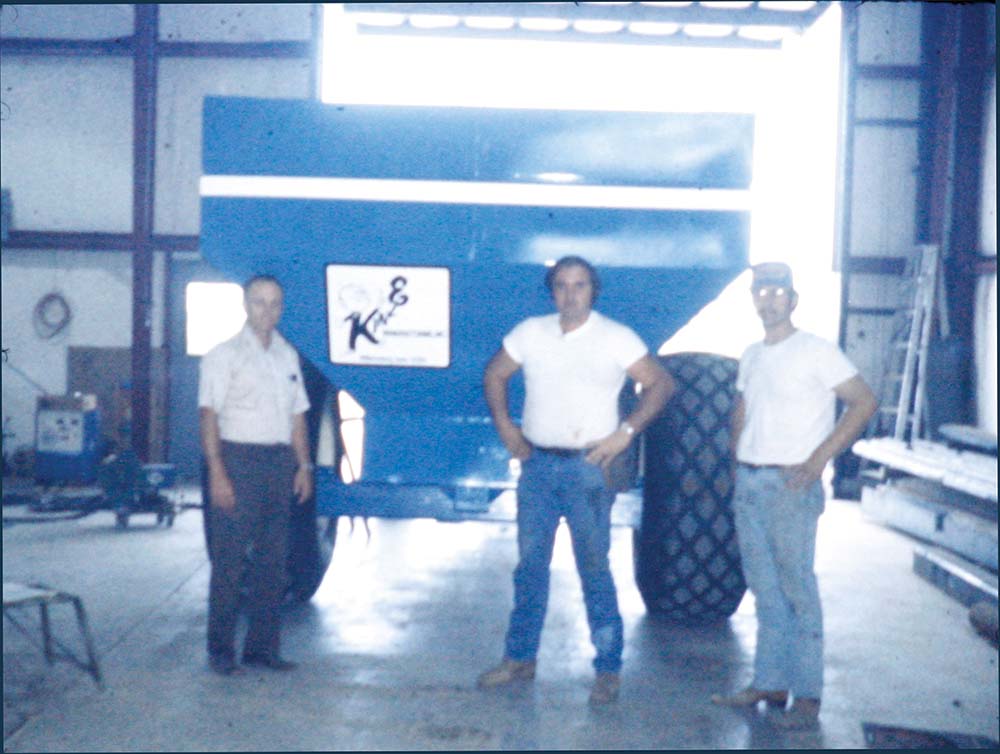
Jon, center, and his brother, Tom, right, with a 400-bushel grain cart
In the meantime, I had licensed the plow to DMI and Bill Dietrich, and during that summer, Bill convinced me to come out to his plant in Goodfield, Illinois, and help him get the plow into production. They needed to get some finished in time for the Farm Progress Show in August at Van Horne, Iowa. That was fine, except I had a problem. I told Bill, “I have a cart that I’m building, and I promised the farmer I’d have it done for the fall corn harvest.” He convinced me that it wouldn’t take long to work on the plow, so I went out to Illinois and began working on it, but one thing led to another and time ran out. We were getting into picking, and Bob needed a cart.
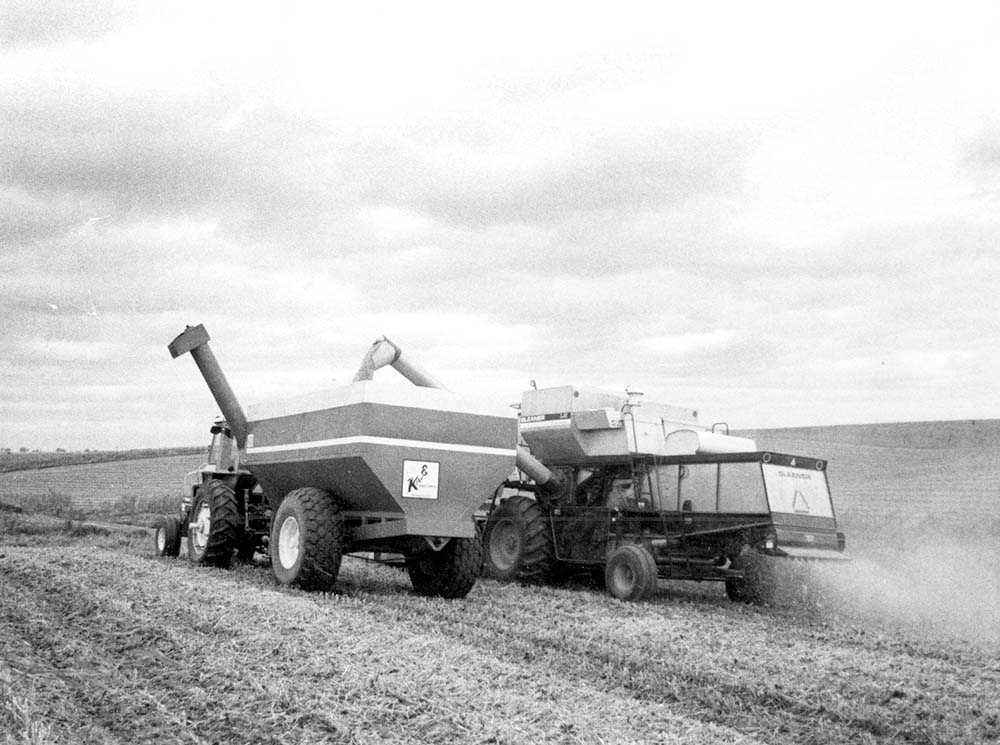
Kinze’s two-wheeled grain cart, which allowed the combine to unload on the go, saved valuable time
At that time, DMI was building four-wheeled, 300-bushel-capacity wagons with a 10-inch auger on the back. It was a far cry from what my two-wheeled cart was going to be, but it would suffice. So we gave that to Bob to use. In October, I got back on the cart and was able to get it finished up. I asked Bob if he cared what color I painted it. He didn’t, and since I’d already painted one of the floaters blue and liked the color, I went ahead and painted the cart blue with white trim and white sideboards on top. It ended up holding 435 bushels, pretty close to what Bob wanted.
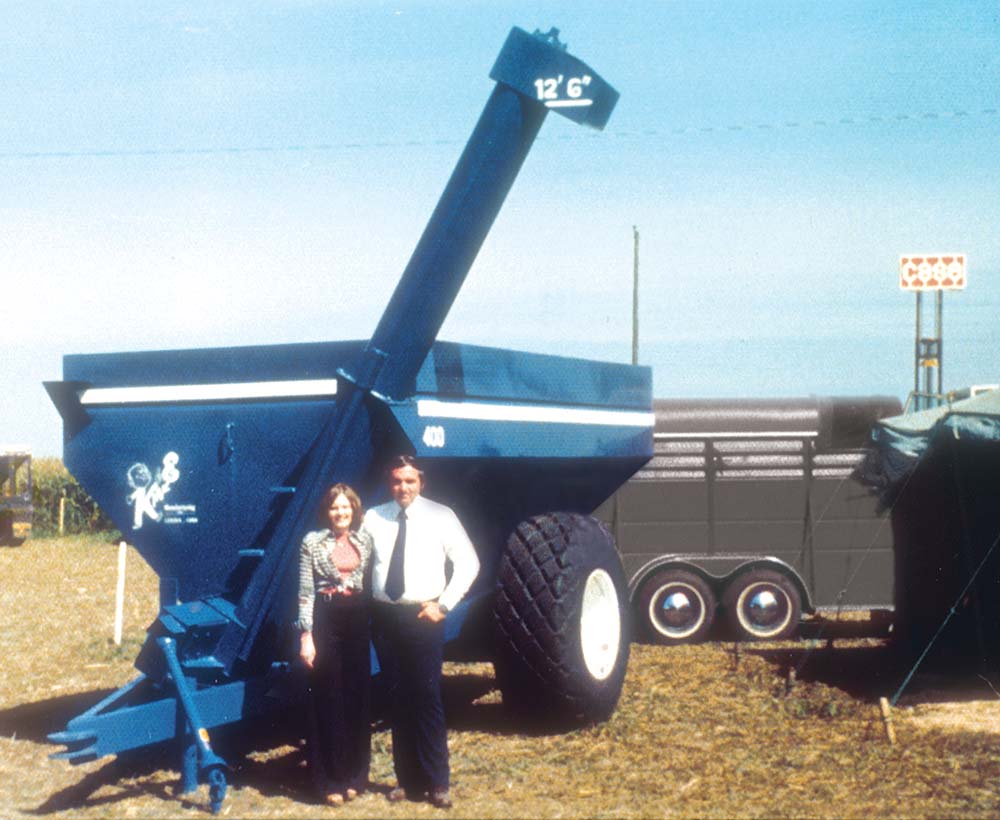
Marcia and Jon with a new grain cart, circa 1974
That cart was basically trouble-free. It just ran and ran and ran. You couldn’t ask for it to work any better, and with those diamond-tread tires, it could go anywhere. I charged Bob $1,700, which meant little, if any, profit. But I was, again, trying to prove I could build something that would do the job. It was such a success, because instantly it made combining a much more efficient process. Without a grain cart, you could lose 50 percent of a combine’s efficiency crossing a field with a full hopper to unload into a truck. A combine with a grain cart worked just as well as two combines harvesting the old way.
There were many advantages. The grain cart was usually a fourth of the price of a truck, and 10 percent of the cost of a combine. The farmer already owned a tractor, and especially if it was a wet year where he needed to use the cart more, he wouldn’t be using the tractor for tillage anyway. Three people — a truck driver, a combine driver, and a grain cart driver — are far more efficient than two people trying to run a truck and a combine, not to mention the wear-and-tear savings on the combine and the truck. It’s very easy to tear the clutch or rear end out of a truck as you try to get it out of the mud. With a grain cart, you can keep the truck on the road. Another huge advantage: the combine doesn’t have to stop harvesting to unload into the cart.
I remember predicting to a farmer that I could envision a day when we could probably build as many as 50 of those carts at a time. Little did I know that it would be just a matter of time before we were building hundreds at a time. As combines got bigger and more efficient, and yields increased, grain carts have substantially increased in size. Our first cart, which became the 440-bushel model, was discontinued because it was too expensive to make for no more than it holds.
The grain carts have been an identity thing for us, even though they consistently represent less than 10 percent of our total sales. Yet when you ask people locally, “What does Kinze build?” they’ll say, “grain carts.”
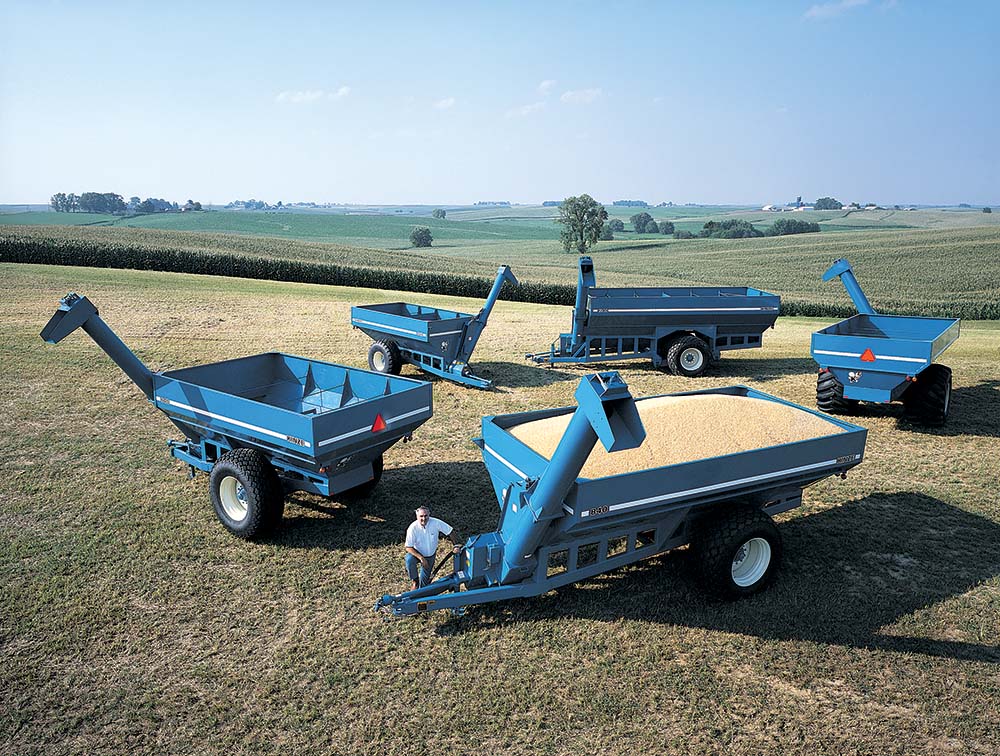